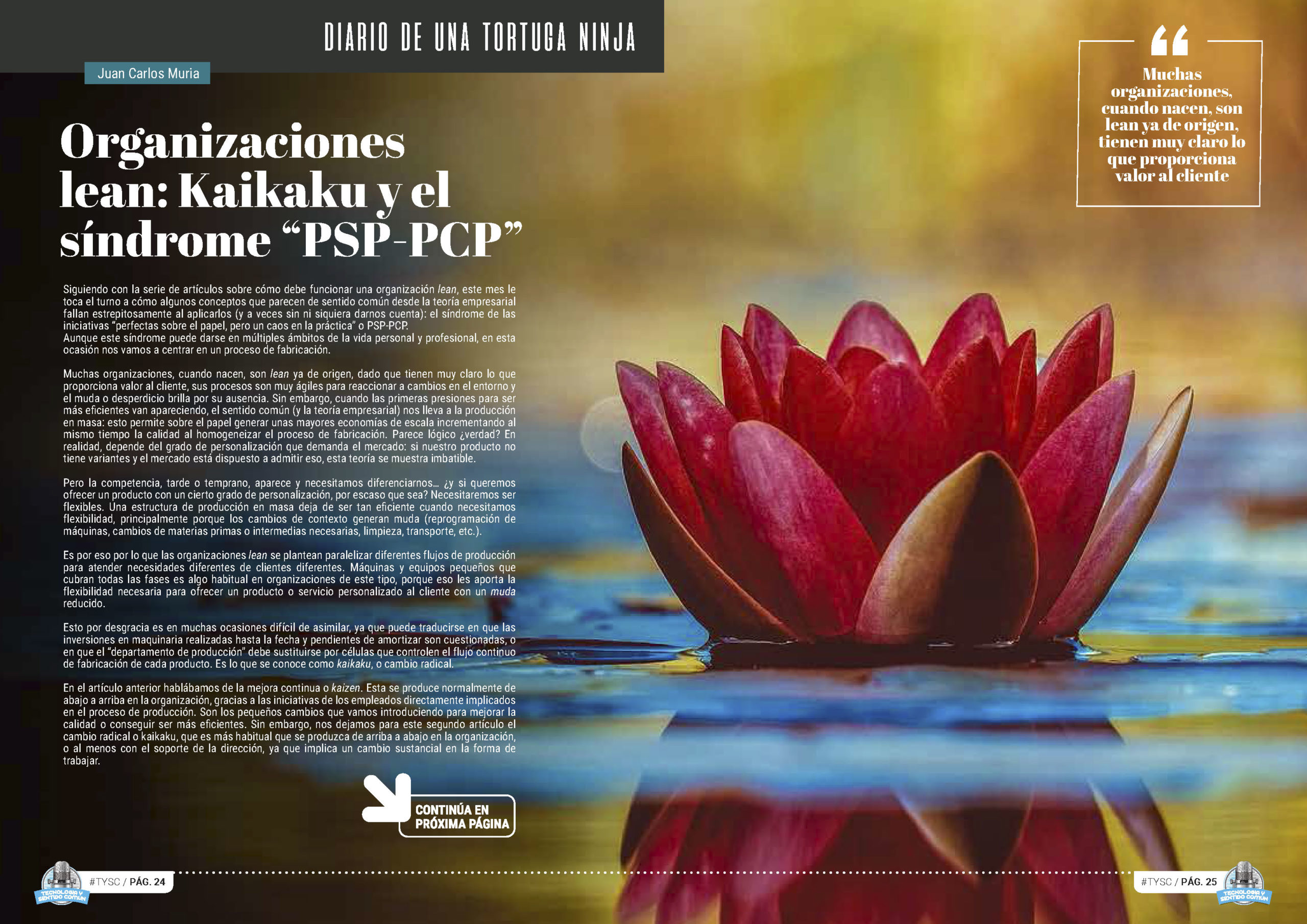
Siguiendo con la serie de artículos sobre cómo debe funcionar una organización lean, este mes le toca el turno a cómo algunos conceptos que parecen de sentido común desde la teoría empresarial fallan estrepitosamente al aplicarlos (y a veces sin ni siquiera darnos cuenta): el síndrome de las iniciativas “perfectas sobre el papel, pero un caos en la práctica” o PSP-PCP.
Aunque este síndrome puede darse en múltiples ámbitos de la vida personal y profesional, en esta ocasión nos vamos a centrar en un proceso de fabricación.
Muchas organizaciones, cuando nacen, son lean ya de origen, dado que tienen muy claro lo que proporciona valor al cliente, sus procesos son muy ágiles para reaccionar a cambios en el entorno y el muda o desperdicio brilla por su ausencia.
Sin embargo, cuando las primeras presiones para ser más eficientes van apareciendo, el sentido común (y la teoría empresarial) nos lleva a la producción en masa: esto permite sobre el papel generar unas mayores economías de escala incrementando al mismo tiempo la calidad al homogeneizar el proceso de fabricación. Parece lógico ¿verdad?
En realidad, depende del grado de personalización que demanda el mercado: si nuestro producto no tiene variantes y el mercado está dispuesto a admitir eso, esta teoría se muestra imbatible.
Pero la competencia, tarde o temprano, aparece y necesitamos diferenciarnos… ¿y si queremos ofrecer un producto con un cierto grado de personalización, por escaso que sea? Necesitaremos ser flexibles.
Una estructura de producción en masa deja de ser tan eficiente cuando necesitamos flexibilidad, principalmente porque los cambios de contexto generan muda (reprogramación de máquinas, cambios de materias primas o intermedias necesarias, limpieza, transporte, etc.).
Es por eso por lo que las organizaciones lean se plantean paralelizar diferentes flujos de producción para atender necesidades diferentes de clientes diferentes. Máquinas y equipos pequeños que cubran todas las fases es algo habitual en organizaciones de este tipo, porque eso les aporta la flexibilidad necesaria para ofrecer un producto o servicio personalizado al cliente con un muda reducido.
Esto por desgracia es en muchas ocasiones difícil de asimilar, ya que puede traducirse en que las inversiones en maquinaria realizadas hasta la fecha y pendientes de amortizar son cuestionadas, o en que el “departamento de producción” debe sustituirse por células que controlen el flujo continuo de fabricación de cada producto. Es lo que se conoce como kaikaku, o cambio radical.
En el artículo anterior hablábamos de la mejora continua o kaizen. Esta se produce normalmente de abajo a arriba en la organización, gracias a las iniciativas de los empleados directamente implicados en el proceso de producción. Son los pequeños cambios que vamos introduciendo para mejorar la calidad o conseguir ser más eficientes. Sin embargo, nos dejamos para este segundo artículo el cambio radical o kaikaku, que es más habitual que se produzca de arriba a abajo en la organización, o al menos con el soporte de la dirección, ya que implica un cambio sustancial en la forma de trabajar.
Licenciado en Informática y Doctor Cum Laude en Organización de Empresas por la Universidad Politécnica de Valencia. Con acreditación en Gestión de Datos para Investigación Clínica por la Universidad de Vanderbilt, ha sido profesor de marketing digital, big data e inteligencia de negocio, y ahora es profesor de Organización de Empresas en la Universidad Politécnica de Valencia. Miembro de la Junta Directiva de la Asociación Valenciana de Informáticos de Sanidad (AVISA), auditor CISA, CGEIT y profesional certificado en ITIL, COBIT 5 y PRINCE 2. Con casi 20 años de experiencia en el sector de la salud, ha dirigido proyectos de interoperabilidad, seguridad y big data, y actualmente es directivo en una importante multinacional de soluciones de TI para el sector de la salud.
Comparte esto:
- Haz clic para compartir en X (Se abre en una ventana nueva) X
- Haz clic para compartir en LinkedIn (Se abre en una ventana nueva) LinkedIn
- Haz clic para compartir en Facebook (Se abre en una ventana nueva) Facebook
- Haz clic para enviar un enlace por correo electrónico a un amigo (Se abre en una ventana nueva) Correo electrónico
- Haz clic para compartir en WhatsApp (Se abre en una ventana nueva) WhatsApp
Debe estar conectado para enviar un comentario.